Case Study: Owner's Engineering
- aladams
- Jan 7, 2020
- 4 min read

“Owner’s Engineering” can elicit varied reactions from people, so before we get to the case study, let’s review Flux’s philosophy on Owner’s Engineering.
Distributed generation projects rely on a property owner to provide a location for new technology. A project developer will define a compensation plan based on a variety of assumptions including impact on the building and project profitability, among others. Refer to previous blog posts to learn more about financing process. As the project gets designed, permitted and built, there are modifications to the original assumptions. For a property owner, that can be confusing since she or he does not have a team dedicated to assessing risks, market trends and technologies specific to clean energy technology. This leaves the building owner dependent upon contractors to make decisions on her or his behalf
That’s where we come in. Flux Energy represents the property owner throughout the project. They can rely on our expertise to make sure their interests are represented in every project decision. Many contractors consider the Owner’s Engineer their adversary, but Flux approaches it differently. We like to encourage a very collaborative working atmosphere. This ensures all project players will have a higher quality and less stressful experience if the whole team is positive and cooperative.
Now to the Case Study!
Flux recently represented a building owner on a 2 MW roof-top solar photovoltaic project. Financing had been secured, and the project had been fully approved by the utility and all permitting authorities. In fact, construction was about to begin when the contractor suggested changing the PV racking to a different system with which he was more familiar and could get the materials at a lower cost. These were very valid reasons to change the racking, but our client did not have the background to understand exactly how the change could impact the project and her building. She requested that Flux review and report back before she approved the change.

Figure 1. Original Racking Configuration as permitted and approved by financing, the utility, the roof membrane manufacturer and the city.

Figure 2. New racking configuration which Flux would evaluate the tilt, spacing, layout and roof attachment methods.
As you can see in Figure 1 and 2, the new racking system was very different from the original. Not only did the module tilt, orientation and spacing change, but the method of attachment to the roof was also different. Flux reviewed against the following categories:
1. Economics Evaluation The economics of a solar project depends upon how much electricity each solar panel makes. Project Developers perform detailed modelling to evaluate the potential for shading and ideal module tilt. As you can see in Figure 3, the two racking systems have very different tilts and shading characteristics.

Figure 3. The new configuration (bottom) has a different tilt from the original (top), so shading, reflection and overall solar generation would change.
2. Engineering Revision As you can see in Figure 4, the two configurations are very different, so the wiring and the location of the racking would change requiring design revisions and an analysis by both the structural and electrical engineers.

Figure 4. A birds-eye view of the two racking variations, clearly showing how drastically different the project layout would be.
3. Permit Resubmittal New designs meant the city’s Building and Safety, Fire and Electrical departments would need to review the plans again.
4. Roof Warranty Assessment As you can see in Figure 5, the attachment methods for the two racking systems are very different as well. The original plan penetrated the membrane to attach directly to the roof structure. The new method does not penetrate the roof surface in any way, but instead sits on top of the membrane. Once the structural engineer evaluated the feasibility of the new design, the roof manufacturer would need to make sure that their warranty would still apply to this installation.
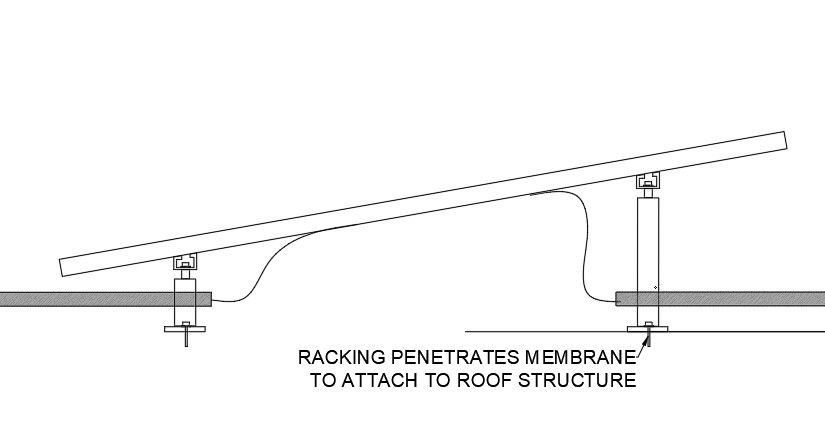
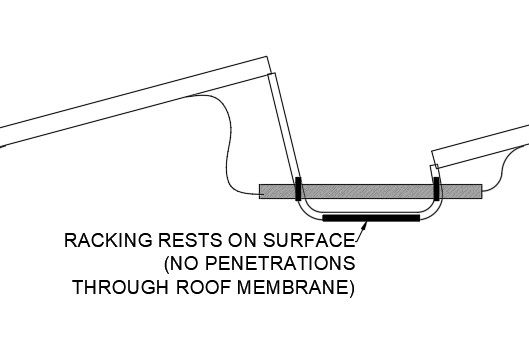
Figure 5. These two images show how the interface with the roof differs between the
two systems.
After reviewing all these factors, we were able to give the property owner a full analysis on the potential impact of the racking change. There was flexibility in the project schedule, so she was not concerned about added time to the project due to redesigns and permitting especially since the contractor would have absorbed those costs. Similarly, generation was minimally impacted by the new module tilt, spacing and shading, so that was not a concern either. However, the roof manufacturer would not extend the warranty to the new racking system! It was a brand-new roof, less than one year old, so the building owner could not sacrifice the roofs warranty for the contractor’s cost savings.
By working with Flux, our client avoided the loss of her roof warranty. In fact, our total fees were probably far less than the cost to repair one leak! When making such a substantial investment, it benefits the property owner to hire a representative to ensure their perspective is represented in every project decision.
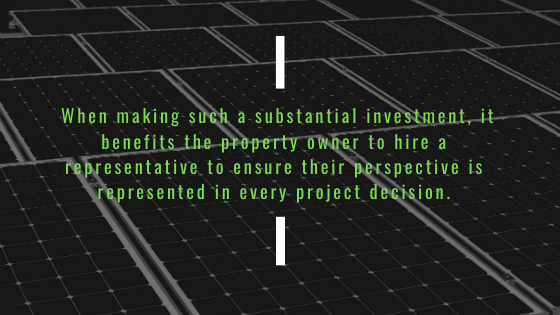
Comments